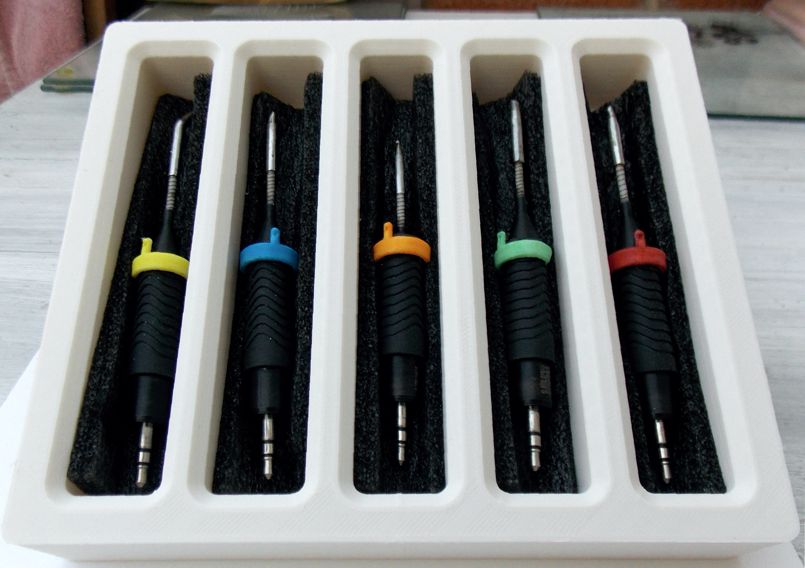
Revolutionizing Precision: A Look into Enhanced Soldering Efficiency
Welcome to the world of soldering, where precision meets innovation. In the meticulous realm of electronics work, having the right tools makes all the difference. Soldering, the process of joining two or more items together by melting a filler metal (solder) into the joint, is foundational yet intricate. However, with the advent of fine soldering tips featuring different shaped profile ends, new challenges have emerged, notably in accurately placing solder and achieving maximum heat transfer. Michael G Parry – Thomas has ingeniously addressed these challenges with his design, introducing 3D printed markers and further innovations to streamline the soldering process significantly.
The Fine Tip Dilemma
The crux of the problem lies in the distinct wx smart shapes of fine soldering tips which, while advantageous for specific tasks, compel the user to employ magnifying glasses just to determine where to apply solder. This precision exercise not only slows down the process but risks improper solder placement, making efficient heat transfer a game of guesswork. Michael’s solution? Ingeniously designed 3D printed markers that identify the optimal side for solder application, thereby eliminating the guess and enhancing accuracy.
Avoiding Wear and Tear
Another overlooked aspect of soldering efficiency is the physical wear on soldering iron tips. Commonly with the Weller soldering stations standcome with a metal bar that, though seemingly innocuous, can easily catch on and degrade the soldering iron tip over time. Michael’s innovative response to this predicament is a silicon roll solution. By ensuring that the soldering tip rolls against a soft cushion instead of scraping against metal, the lifespan of the iron tip extends, maintaining its pristine condition and functionality.
Combating Dust Accumulation
Dust and debris accumulation presents a subtler yet significant threat to soldering stations, particularly within unused channels. This seemingly minor issue can lead to decreased performance and lifespan of the equipment. Enter Michael G Parry – Thomas’s design solution—channel caps. These dust covers are specifically tailored to protect the soldering station’s channels from dust buildup when not in use, thus preserving the station’s efficiency and longevity.
Conclusion: A Leap towards Soldering Perfection
In conclusion, Michael G Parry – Thomas’s contributions to the soldering community are nothing short of revolutionary. From the introduction of 3D printed markers for enhanced accuracy in solder placement to the design of a silicon roll for reducing tip wear, and finally, channel caps for dust protection, each innovation speaks to a deep understanding of the nuances in soldering practice. These advancements not only address existing challenges head-on but also pave the way for a future where precision soldering can be achieved effortlessly and with greater accuracy. As we embrace these innovations, the landscape of electronic work is poised for unparalleled efficiency and efficacy.
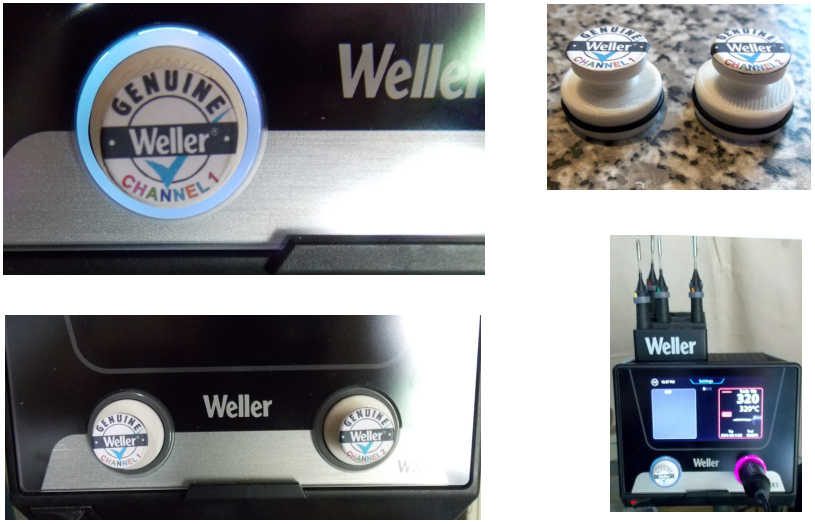
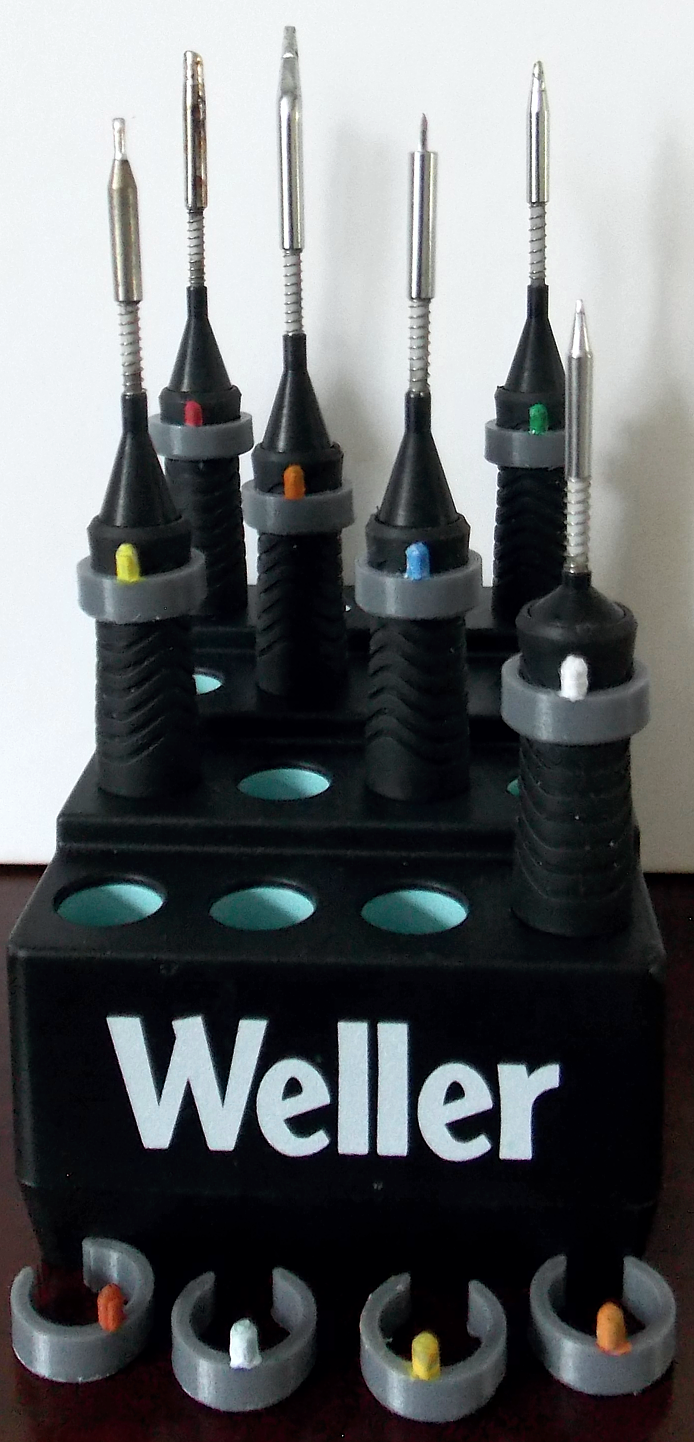
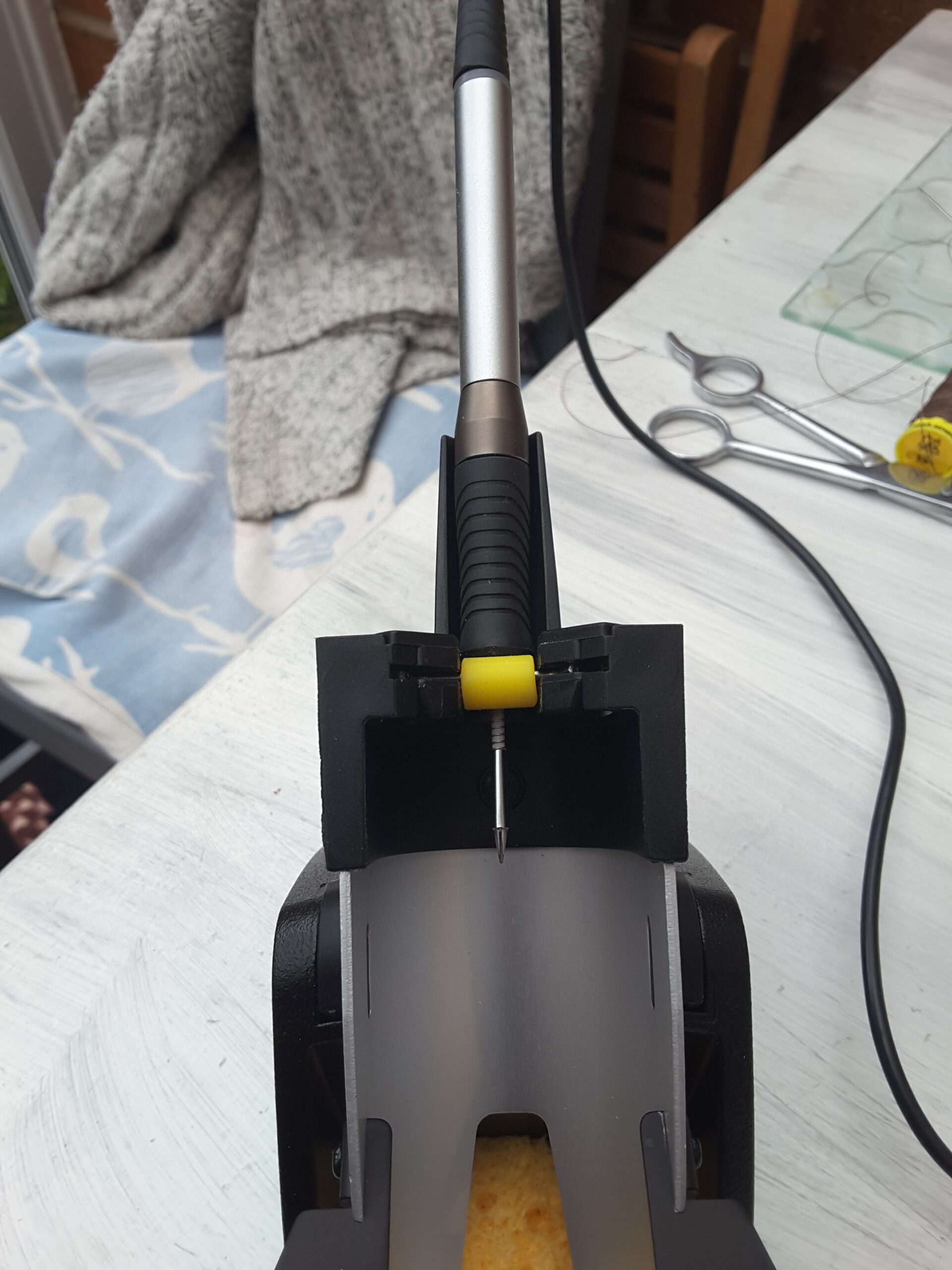
I have recently made some refinements to the design of the soldering tip alignment marker. In this updated version, the clips have been improved by eliminating sharp edges, resulting in a streamlined appearance. Additionally, the clip now sits higher on the shoulder of the rubber grip of the soldering tip, and the clips are now in bright colors for better visibility.
Furthermore, I have also designed dust covers that can be inserted into any of the channels on the soldering station that are currently not in use. These dust covers play a crucial role in safeguarding the soldering station ports from any debris and dust that may accumulate during soldering activities. As it is common to encounter fine particles of debris while soldering, it is a practical approach to protect any unused soldering ports or those that do not have a tool connected to them. This added feature will enhance the longevity and cleanliness of the equipment.
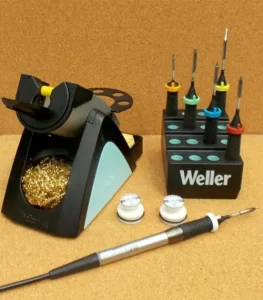
Prototype Oscillating tip cleaning box
soldering tip cleaner
Throughout the soldering process, I’ve encountered various situations where it becomes necessary to clean the soldering tip in order to eliminate any burnt carbon flux residue that accumulates. Maintaining a clear tip significantly enhances the quality of the solder joint, which prompted me to create an oscillating tip cleaner specifically designed for my very fine soldering iron tips. Whenever a deep clean is required, all I need to do is draw the tip down between two brushes that are arranged to allow an oscillating movement as the tip passes between them. This design provides a gentle cleaning action, effectively removing solder and burnt solder flux residues. Additionally, any particles of solder that are dislodged collect at the bottom of the box for easy disposal. Notably, this mechanism for oscillation does not incorporate any electronic components; instead, it utilizes a purely mechanical system to achieve the desired effect.
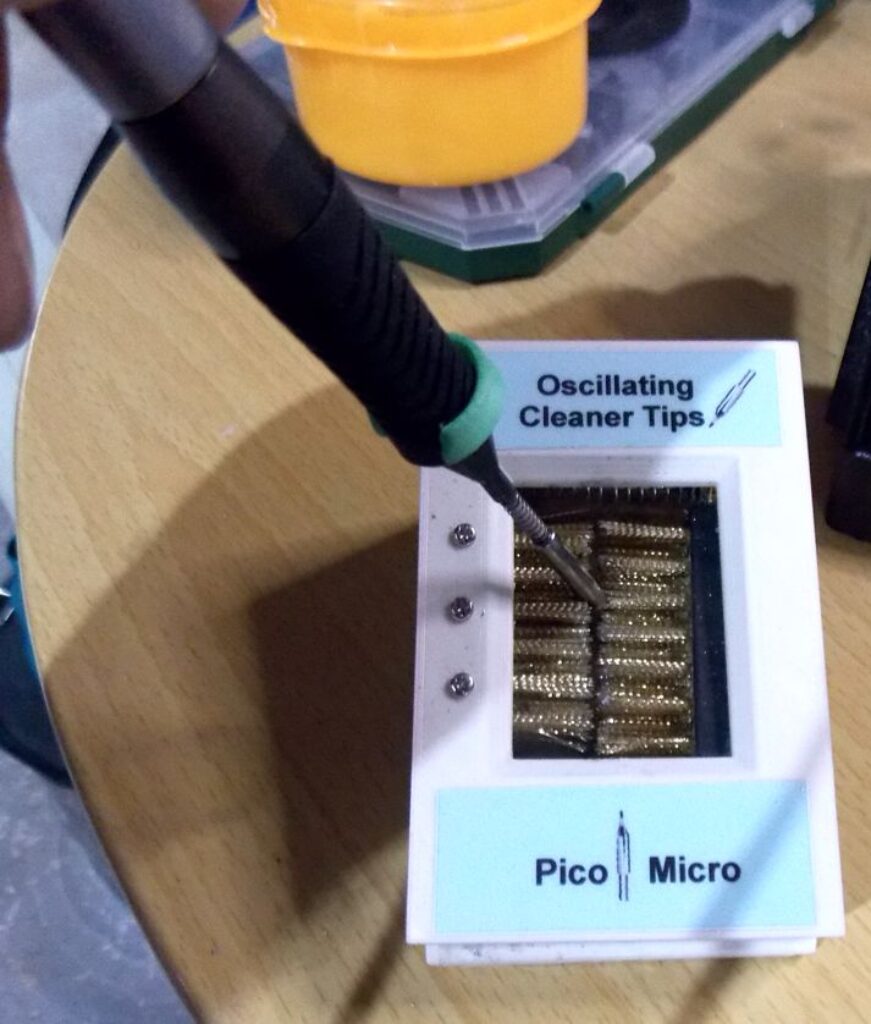
Universal Tip Cleaner
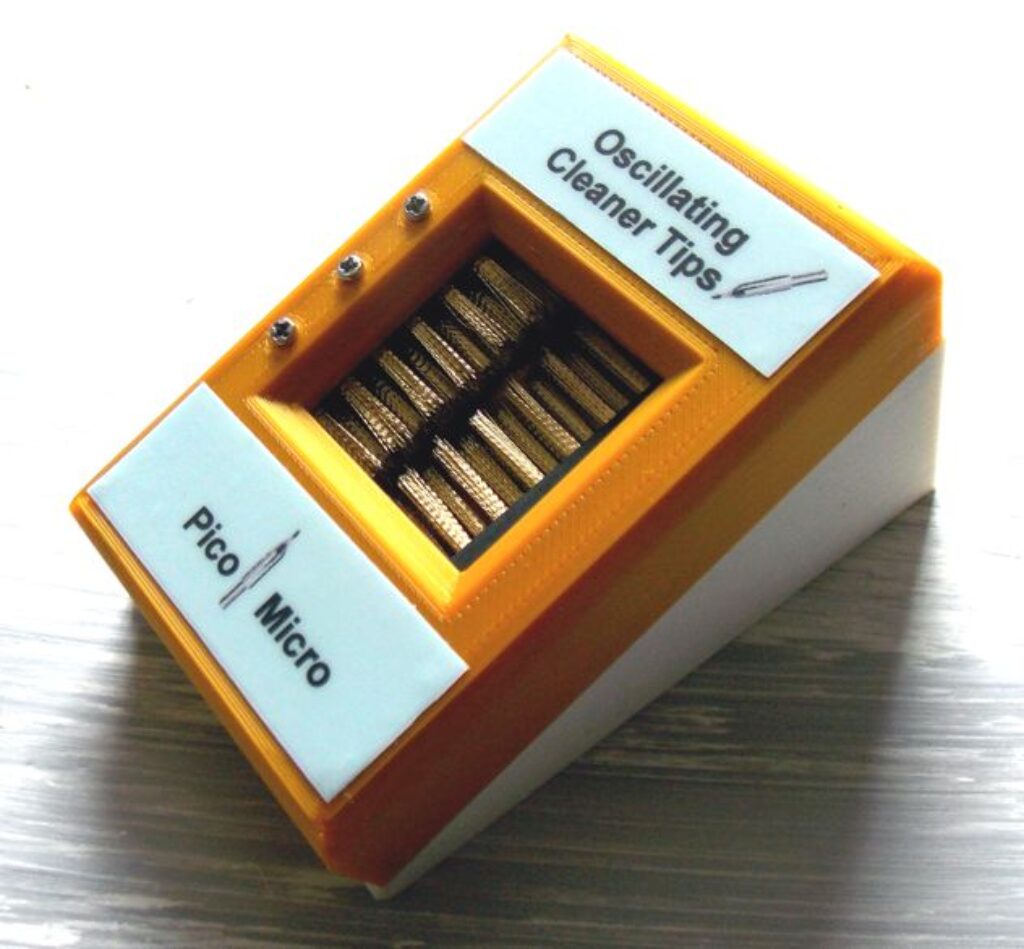
Soldering tip cleaner using mechanical oscillating system
WX Smart Soldering Tip organiser Box
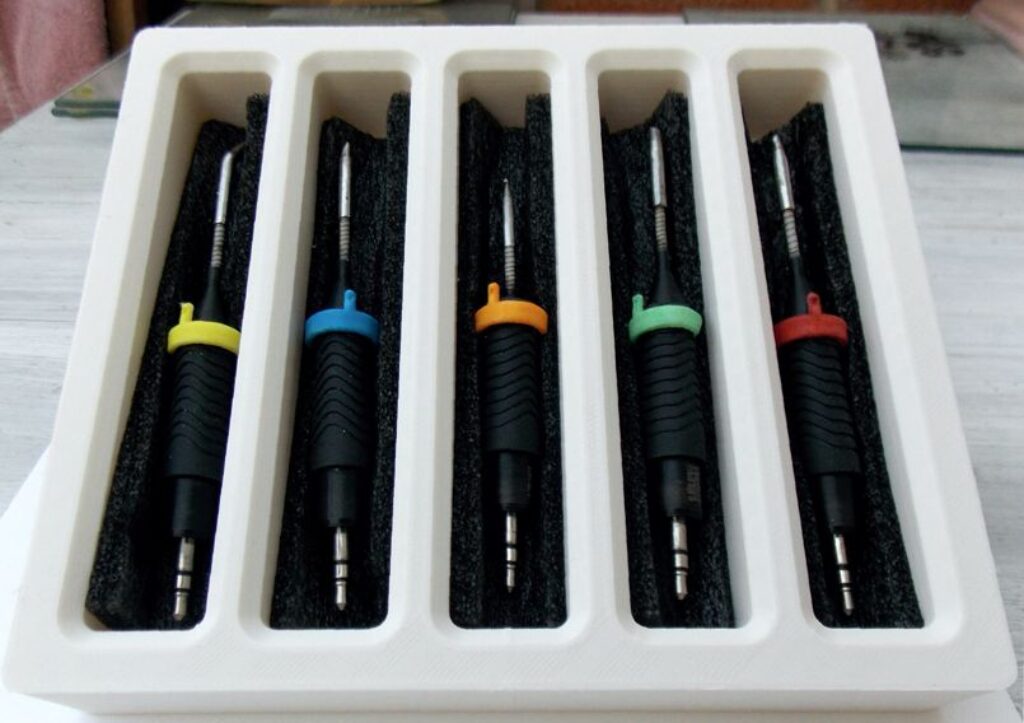
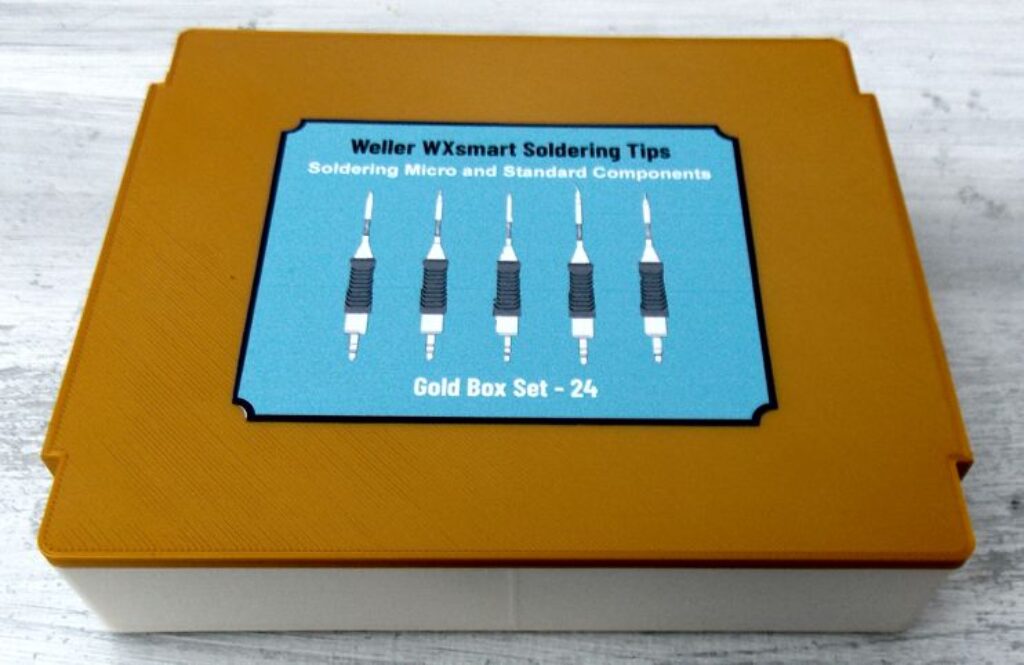
designed by Michael G Parry-Thomas